Over the past 70 years, the skateboard has been on quite a ride. It first emerged in 1950s Los Angeles as a humble, homemade toy, but, before long, it became a bona fide cultural phenomenon — spawning skate parks, street style and video games before, finally, becoming an Olympic sport at the 2020 Games.
The global value of the skateboard market has also sped along, with the data gathering service Statista projecting total worldwide skateboard sales to hit $2.26 billion this year.
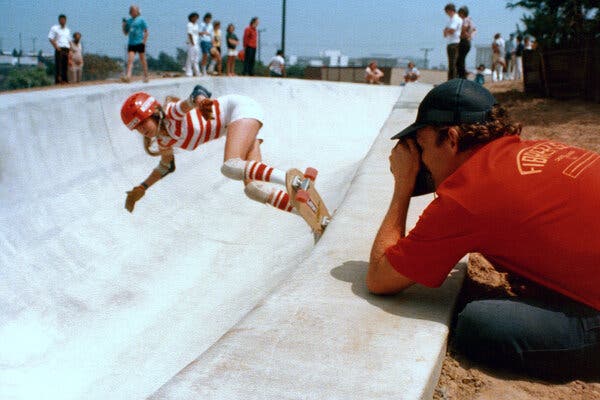
As the board has gained fans, the craftsmanship behind it has also evolved, one focus of “Skateboard,” an exhibition at the Design Museum in the Kensington district of London (through June 2). The show charts the evolution of the board’s design from 1953 to 2023, in the form of 96 skateboards and skate decks; skateboard components; and gear.
According to Jonathan Olivares, the industrial designer and skateboarder who curated the exhibition, which was sponsored by the brand Converse, the boards on display were chosen because they represent major advances in design and performance. The 1969 Makaha LX 10, for example, “enabled the first tricks that were native to the skateboard, not just lifted from surfing,” he said, and it was the first board to have a kick tail, an innovation pioneered by Makaha’s founder, Larry Stevenson. That upward curve at one end of the board, Mr. Olivares explained “allows you to pivot on the back wheels.”
There also is a deck that Unity Skateboards, a queer skateboard collective in California, created this year, featuring a figure sitting on the shoulders of another pink figure with words reading, clockwise: “LIKE IT OR NOT!!! UNITY TOGETHER AS ONE UNITY.”
Mr. Olivares wrote in a later email that Unity Skateboards is “the first skate brand that is founded by an LGBTQIA+ skate crew, and that creates a space for LGBTQIA+ skaters in the market.”
Emotional Ties
So while there is a practical aspect to the skateboard — namely, helping someone to move from Point A to Point B — the existence of makers like Unity Skateboards reflects the emotional ties many enthusiasts have to their boards. For 29-year-old Matty de Vere, the founder of Big Aye Skateboards in London, his company name and logo spring from his roots in Hexham, in northeast England. He explained that the word “aye” means “yes” in Northern England and Scotland and is often used there.
Todd Huber, 58, explained that skateboards are “part of my culture,” like cricket bats are for the English.
Mr. Huber, who founded the Skateboarding Hall of Fame and Museum in Simi Valley, Calif., in 1997, added: “For a guy like me, who is a loner, who doesn’t want to be on a team with somebody,” having a skateboard “gave me something that I was good at and was fun and got me active.”
Skateboards also have historical importance, according to Jane Rogers, a curator specializing in sports at the Smithsonian’s National Museum of American History, which has a skateboard collection. She was also a co-editor of “Four Wheels and a Board: The Smithsonian History of Skateboarding.”
Each board, Ms. Rogers wrote in an email, “tells a particular story, whether it be about the person who made it, the person who used it or what is depicted on its surface or what it’s made of.” Case in point: Paisley Skates’s Paisley Grabs Back design, showing people in pink pussy hats at the 2017 Women’s March, held in Washington the day after President Donald J. Trump’s inauguration.
In the 1950s, Ms. Rogers explained, the first skateboards were cannibalized from wooden scooters and surfboards. Later on, the process of making boards evolved, as materials like resin, fiberglass and plastic began to be used for decks in the late ’60s, and maple plywood appeared in the late ’70s. It continues to be a popular choice to this day.
But board builders today, like Tim Snel, owner of Timber Boards in Leeuwarden, the Netherlands, are continuing to experiment with materials.
Mr. Snel, 33, starts with some bamboo grass, then alternates layers of fiberglass and carbon fiber to build up the deck, finishing with a thin bamboo veneer printed with a graphic design. He said he chose bamboo because it is fast-growing and sustainable, and chose fiberglass for its strength.
“The amount of flex is kind of determined by the amount of carbon fiber and glass fiber that you put in the board,” he said, explaining that “bamboo by itself isn’t stiff enough” to bend repeatedly without becoming very soft.
“A Lot of Trial and Error”
Some skaters have started making their own boards, like Mark Smith, 40, who in 2017 founded Gully Boards in his father’s garage in Boronia, a suburb of Melbourne, Australia. He has been working alone, making skateboards from recycled timber and sustainably sourced timber, ever since.
He named the business Gully Boards after Ferntree Gully, the nearby city where he grew up, and the Gully Boardriders, his former skateboarding crew. He and two other members of the group still skateboard, but, he said, “with the onset of kids and other things, it becomes a little harder to get out.”
Mr. Smith, a former advertising executive and semiprofessional ice hockey player, said that he taught himself to make boards, learning the craft from YouTube videos; from his father (who retired from being a carpenter, but still cuts wood for him); and from what he described as “a lot of trial and error.”
He constantly searches for timber, and gets some supplies by working for a friend’s carpentry business from February to April, when customers are recovering from the busy holiday shopping season, so his own operation is not busy.
In 2021, for example, Mr. Smith and his friend replaced a front porch in Melbourne, so he was able to salvage lumber from the project. It was reddish wood from the tall eucalyptus tree, called jarrah, which grows across southwest Australia. He then used it to create the Jarrah Cruiser, with an inlay made from recycled Victorian ash. The finished board is 95 centimeters (about 3 feet) long, with a pin tail, the sport’s term for a narrow rear end, and sells for 435 Australian dollars ($276).
Some woods are easier to work with than others, Mr. Smith said. Victorian ash, which grows in Australia’s southeastern state of Victoria, usually has a straight grain, so a saw blade or router “is able to cut around that corner smoothly,” he said. Spotted gum, however, a wood found in eastern parts of the country, has a short grain that is not always straight.
Getting the thickness of the wood right is the greatest challenge, he said, so several times he feeds each piece through a planer, called a thicknesser in Australia, which shaves off a fraction of a millimeter each time.
His process has several key steps: cutting wood to length and width, gluing three pieces together, side by side, and then, using a router, shaping that whole piece into a deck (and drilling eight holes for the hardware), sanding and then oiling it all. When the oil is dry, he adds the trucks and wheels, which he buys from manufacturers in China.
For the board’s decorative accents — diagonal stripes running across the lower half of the board — Mr. Smith uses the router to cut channels about four or five millimeters (a tenth to two-tenths of an inch) into the surface of the board, then places thin strips of wood, with glue on the bottom, into the channels, knocking them into place with a rubber mallet.
Mr. Smith said he had to experiment to find the right oil to protect his boards from moisture damage and other potential problems, opting for a fast-drying hard-wax oil and then adding a second coat of a clear anti-slip oil (designed for flooring and stairs) all over the board, to give the rider an extra strong grip.
“If there’s any imperfections that I find after the first coat of oil,” he said, “I’ll give it a light sand to remove those imperfections and then I’ll oil again.”
Mr. Smith’s Gully Boards come in three sizes, along with a junior version, designed for children. For example, he makes a small cruiser board of Victorian ash with a V-tail, the term for a notched rear end, that is 75 centimeters long by 18 centimeters wide (about 30 inches long by 7 inches wide) and sells for 275 Australian dollars (about $175). And there is a cruiser made of New Zealand kauri wood — salvaged from a dental office renovation in Preston, a suburb of Melbourne — which has a flat tail, is 110 centimeters by 18 centimeters and sells for 425 Australian dollars.
Most of his boards are sold online to local customers, although they are also carried by retailers like Nash + Banks, which has a store in Avalon, north of Sydney. He does not accept orders from abroad as “it’s just too expensive to ship such a large product overseas,” he said, also noting that there might be customs charges, too.
Mr. Smith does have expansion plans, however. He intends to build a new workshop in his own garden during the next six months, so, he said, he can “make some other products,” like push-up bars, free weights and other exercise equipment.
This post was originally published on this site be sure to check out more of their content.